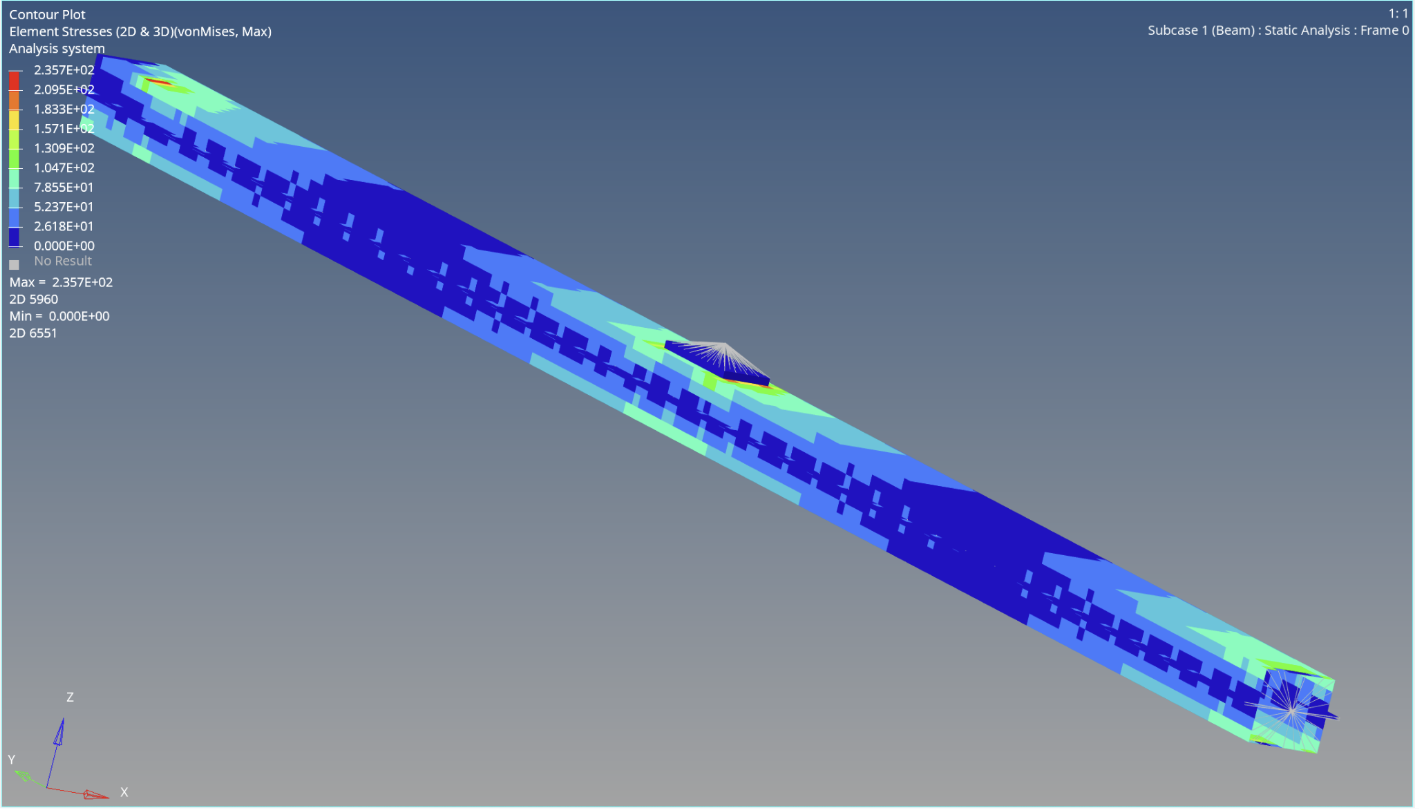
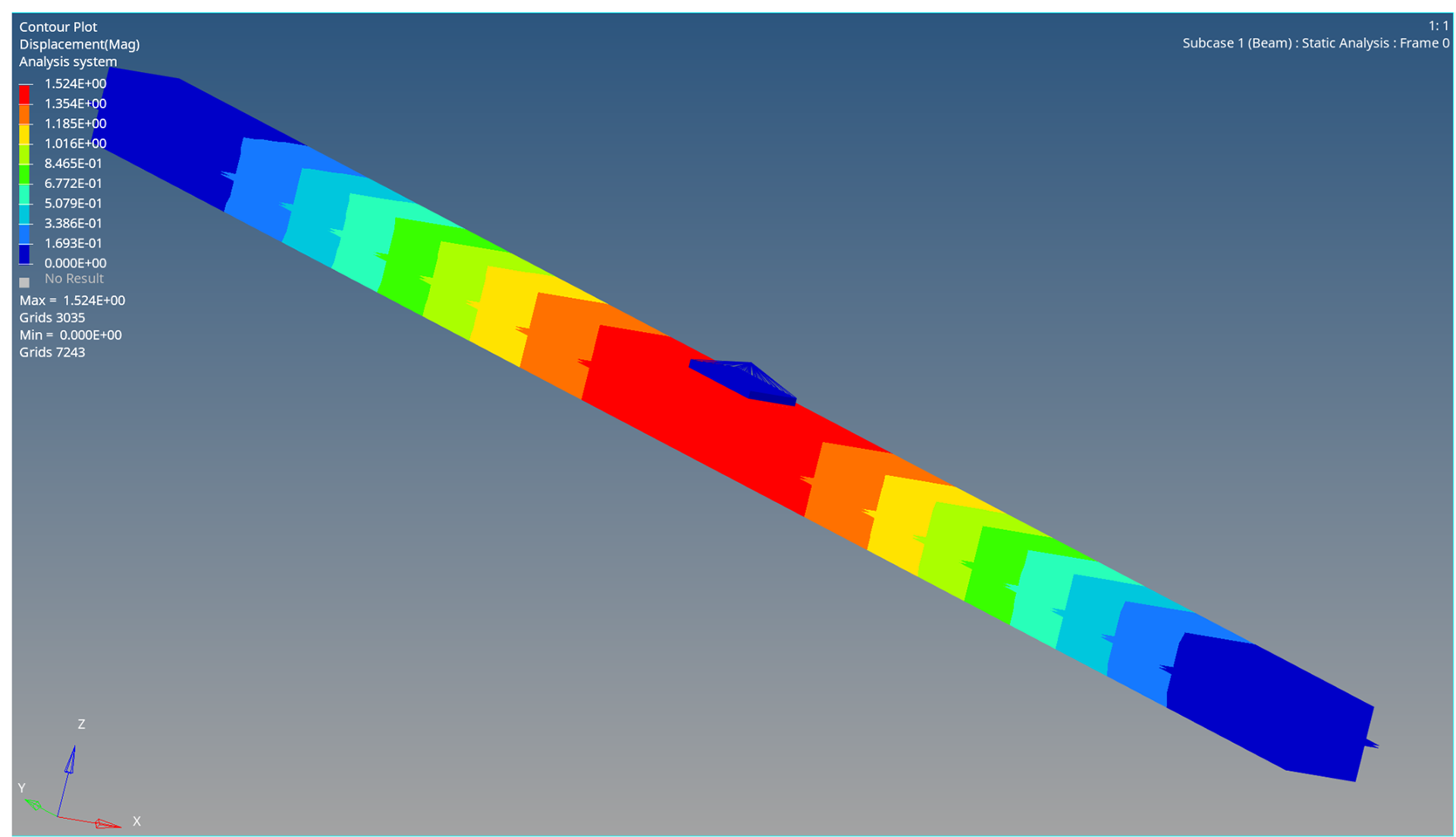
Design and Analysis of a Front Motor Compartment Cross Member
The project focused on designing and analyzing a front motor compartment cross member, a critical structural component that supports the hood latch and enhances vehicle rigidity and safety. The goal was to ensure the cross member could withstand a 1000N aerodynamic load at high speeds while minimizing deflection and maintaining structural integrity.
Key Activities and Results:
Selected a material with a yield strength of 210 MPa and defined properties (modulus of elasticity: 210 GPa, Poisson's ratio: 0.3, density: 7.85 x 10³ kg/m³) for FEA.
Developed 1-D and 2-D FEA models using HyperMesh, employing CBEAM, CQUAD, and CTRIA elements to simulate stress distribution and deflection.
Applied a 1000N vertical load at the hood latch and set fixed boundary conditions to replicate real-world constraints.
Conducted simulations, revealing a maximum stress of 235.7 MPa (exceeding yield strength) and a maximum deflection of 1.698 mm (within the 3 mm limit).
Proposed design improvements, including using a stronger material (yield strength > 235 MPa), increasing cross-sectional thickness, and adding fillets or reinforcements to reduce stress concentrations.
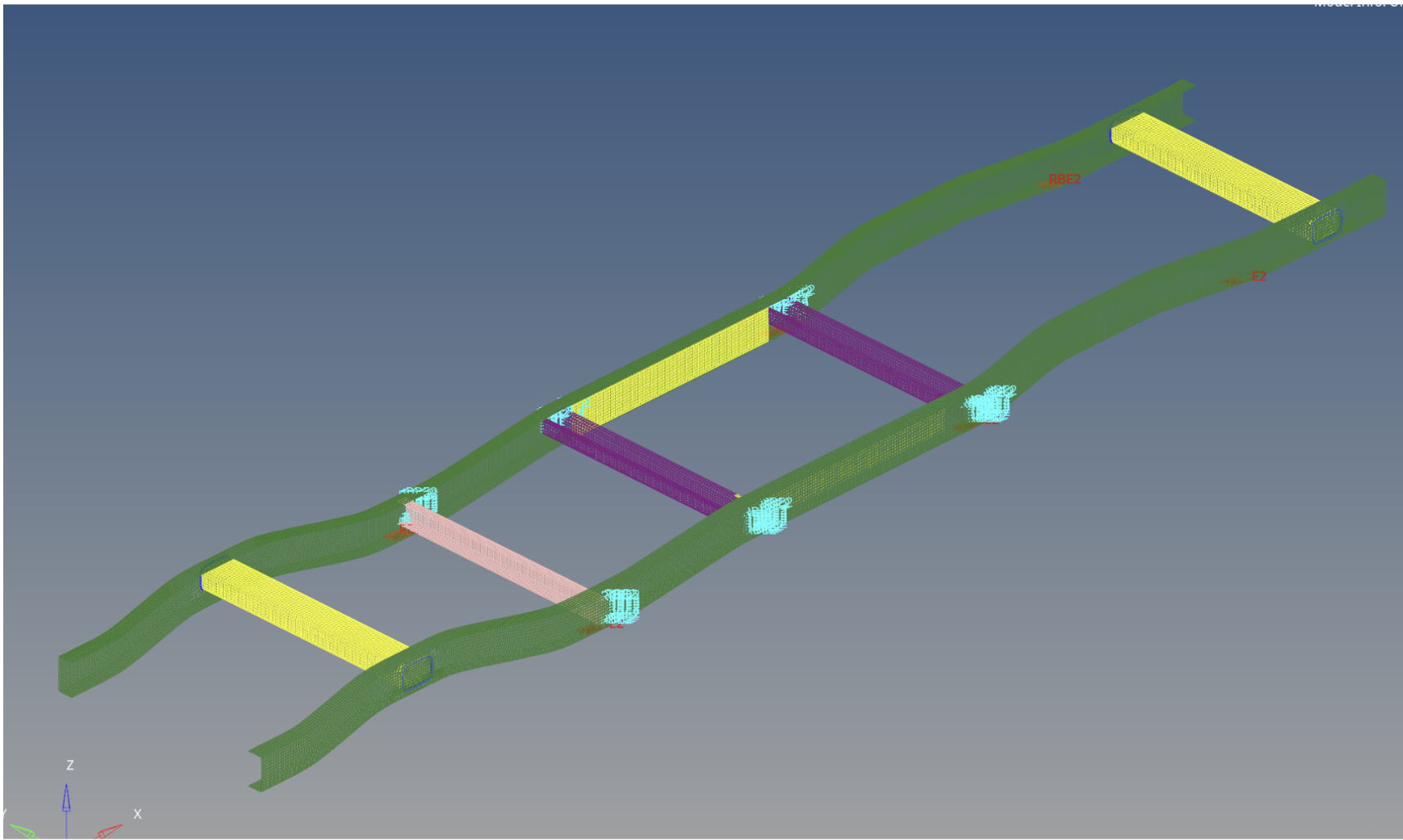
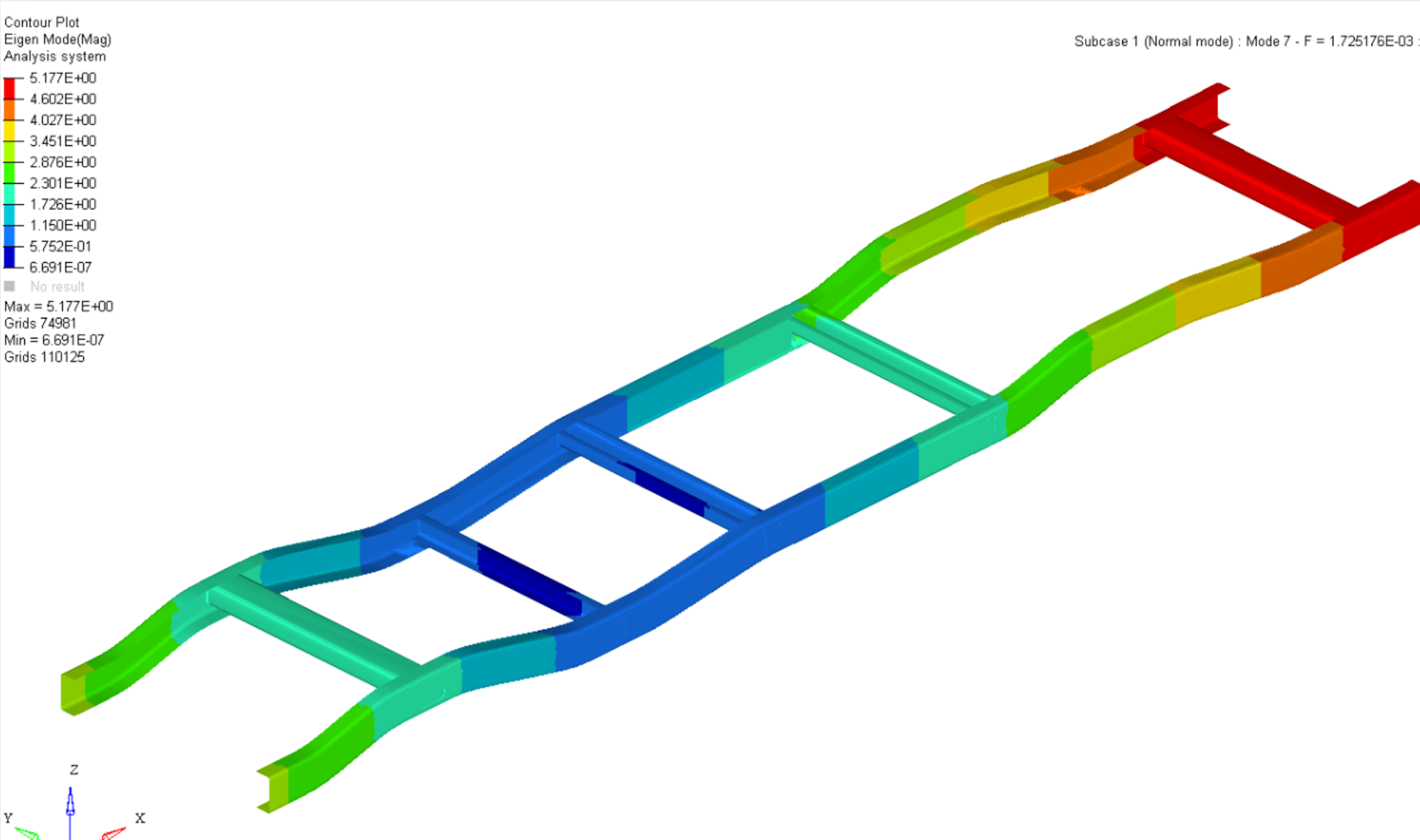
Natural Frequency Optimization of a Frame Structure
The project aimed to analyze and optimize the natural frequencies of a frame structure, focusing on increasing the first natural frequency by 1 Hz to enhance vibration resistance and structural performance.
Key Activities and Results:
Imported and preprocessed the finite element model in HyperMesh, assigning steel material properties (Young's modulus: 210 GPa, Poisson's ratio: 0.3, density: 7.9e-9 ton/mm³).
Conducted normal mode analysis using OptiStruct to identify the first natural frequency and corresponding mode shape, revealing areas of highest deformation.
Proposed and implemented design modifications, including adding stiffeners to the mid-section of the frame, targeting high-deformation areas.
Iterated the analysis and design changes, successfully increasing the first natural frequency by slightly more than 1 Hz, exceeding the project target.
Demonstrated the effectiveness of stiffeners in optimizing the frame’s dynamic performance and vibration resistance
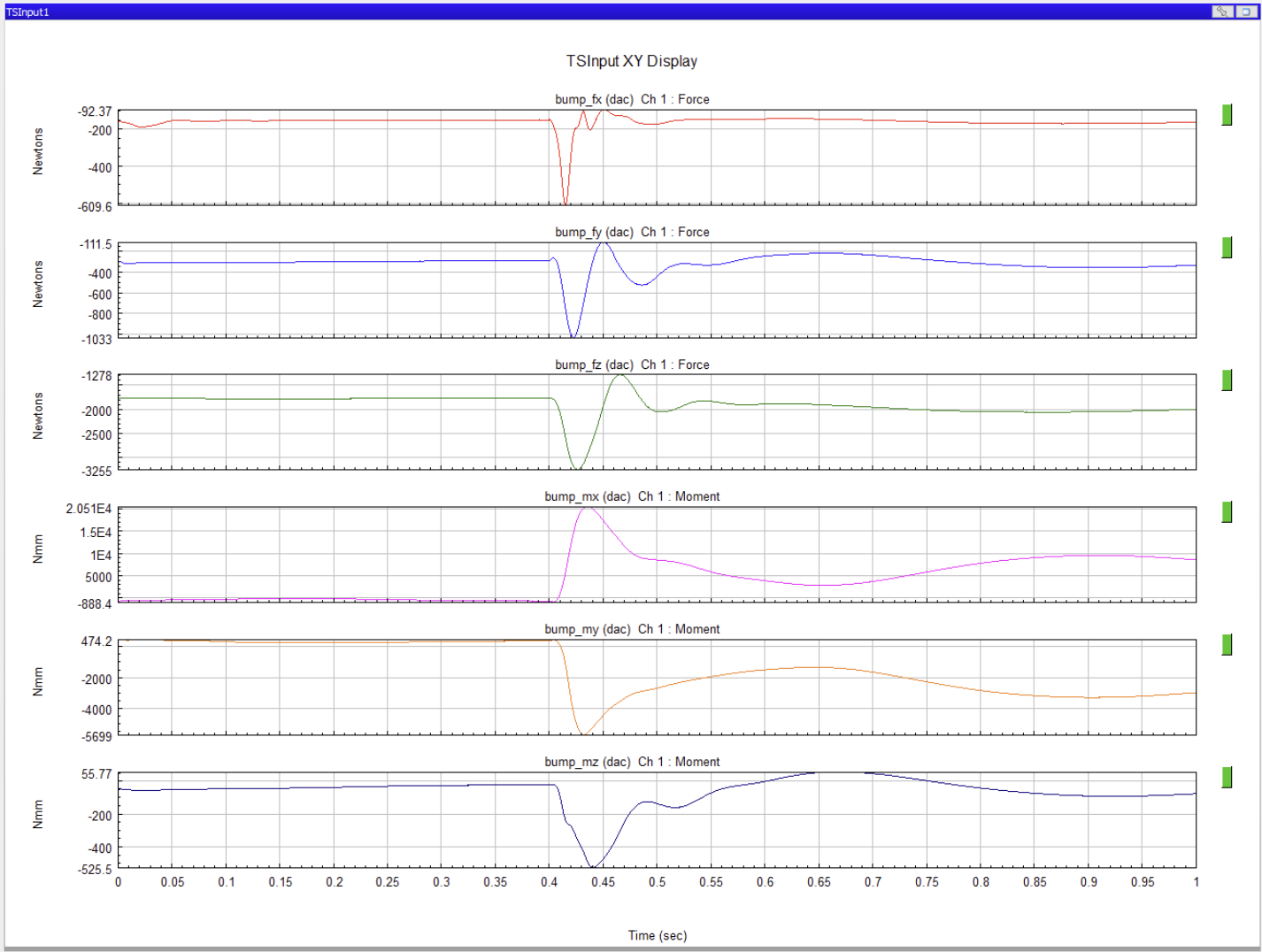
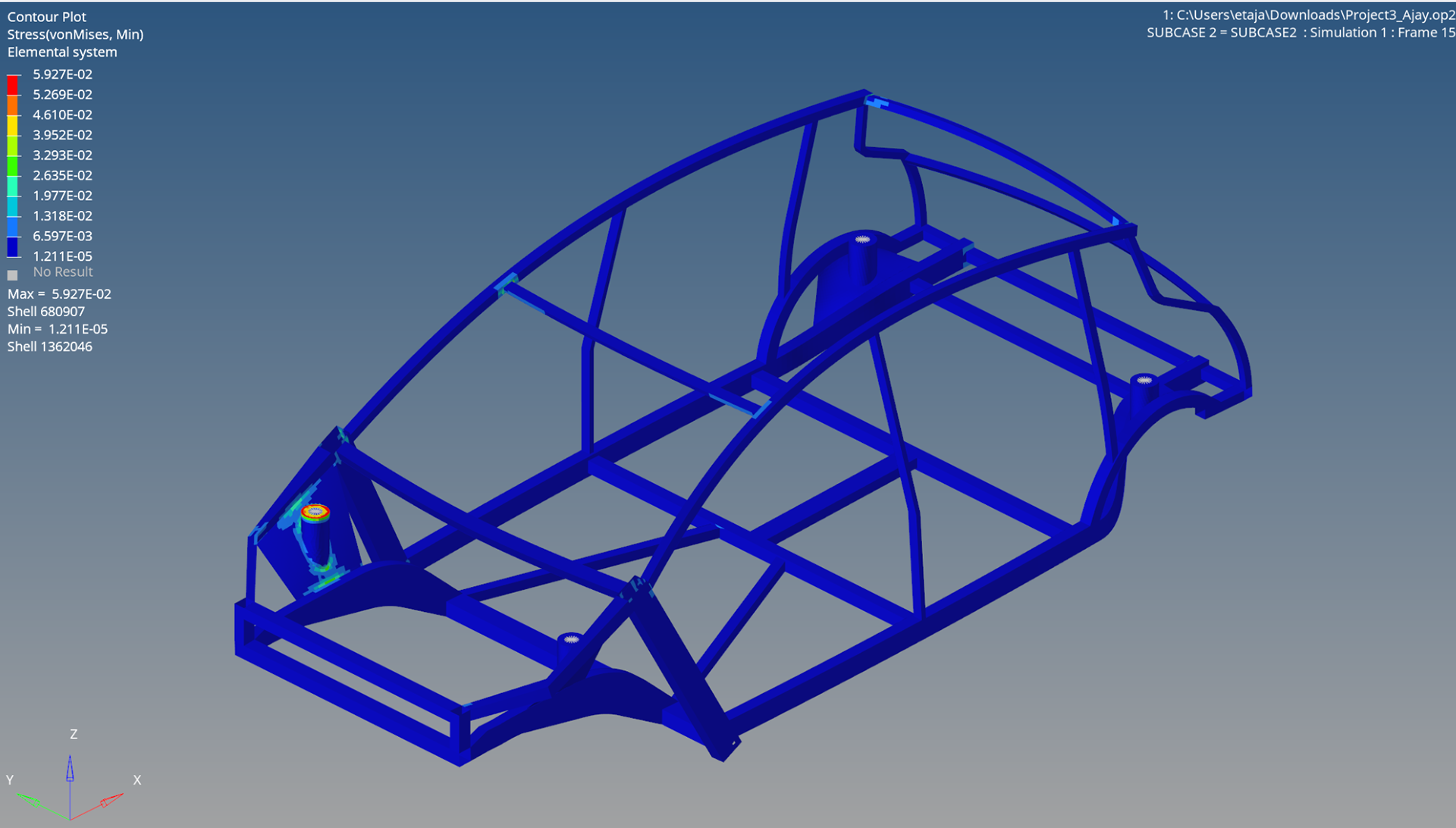
Fatigue Life Analysis and Optimization of a Vehicle Structure
The project aimed to predict and improve the fatigue life of a vehicle structure subjected to fluctuating operational loads, ensuring long-term durability and reliability. Using the S-N approach with Goodman’s equation for mean stress correction, the project identified weak points and proposed design modifications to enhance structural performance.
Key Activities and Results:
Conducted fatigue analysis using NCODE DesignLife, applying the S-N approach and Goodman’s equation to predict high-cycle fatigue life under 1000 simulated load cycles.
Evaluated von Mises stress results from HyperMesh to identify high-stress regions prone to fatigue failure.
Proposed design improvements, including material upgrades (high-strength steels, aluminum alloys, composites), load path optimization, and boundary condition adjustments to reduce stress concentrations.
Implemented and validated design modifications, such as adding reinforcements to high-stress areas, significantly improving fatigue life.
Demonstrated the ability to combine stress analysis and fatigue analysis for a comprehensive evaluation of structural performance under cyclic loading.
Outcome:
Successfully predicted fatigue life and identified critical failure points, enabling targeted design improvements.
Enhanced the vehicle structure’s durability and reliability, reducing the risk of fatigue-related failures.